Comprehensive Overview: What is Porosity in Welding and How to Prevent It
Comprehensive Overview: What is Porosity in Welding and How to Prevent It
Blog Article
The Science Behind Porosity: A Comprehensive Overview for Welders and Fabricators
Recognizing the complex systems behind porosity in welding is important for welders and makers aiming for impressive craftsmanship. From the structure of the base materials to the details of the welding procedure itself, a multitude of variables conspire to either worsen or relieve the visibility of porosity.
Comprehending Porosity in Welding
FIRST SENTENCE:
Examination of porosity in welding reveals crucial insights into the integrity and high quality of the weld joint. Porosity, characterized by the presence of cavities or spaces within the weld steel, is a typical worry in welding processes. These spaces, if not effectively attended to, can endanger the architectural stability and mechanical properties of the weld, leading to potential failings in the completed item.
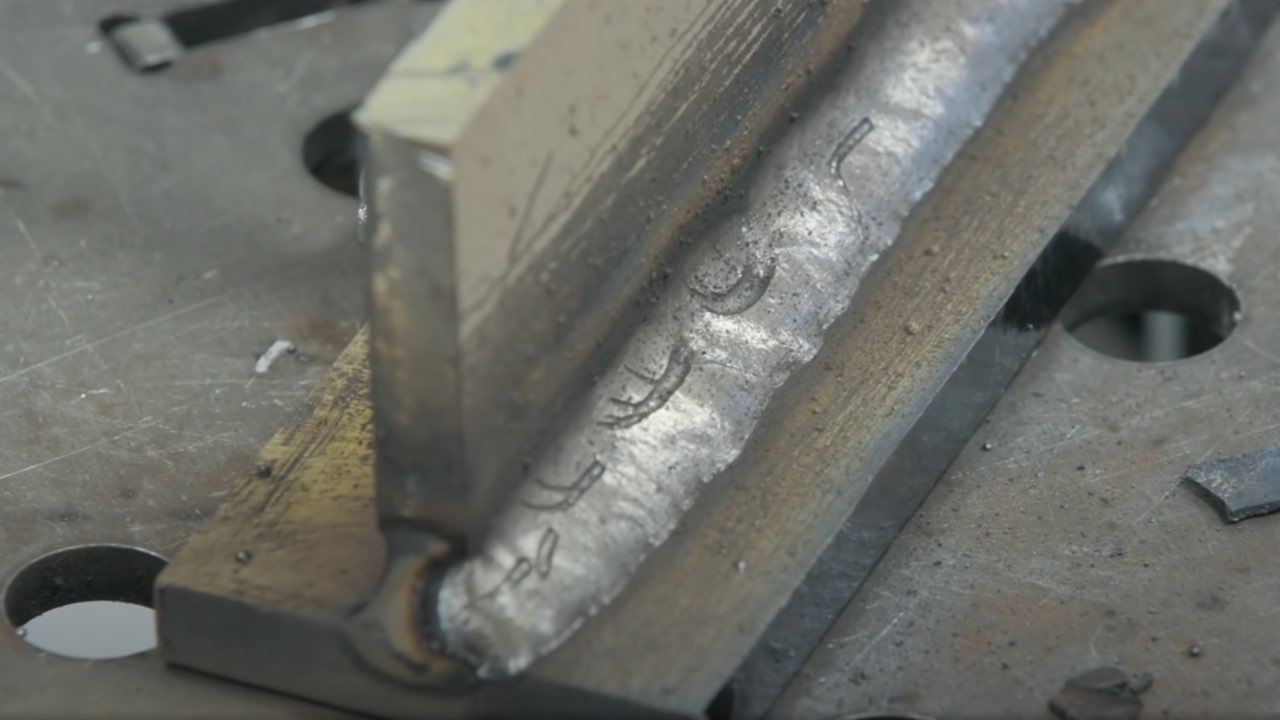
To discover and measure porosity, non-destructive testing approaches such as ultrasonic screening or X-ray inspection are typically employed. These strategies allow for the recognition of inner problems without compromising the stability of the weld. By analyzing the dimension, shape, and distribution of porosity within a weld, welders can make informed choices to enhance their welding procedures and achieve sounder weld joints.
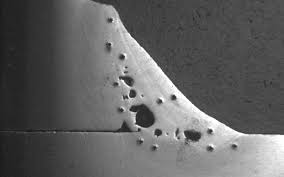
Variables Affecting Porosity Formation
The event of porosity in welding is affected by a myriad of aspects, varying from gas shielding efficiency to the details of welding parameter settings. Welding parameters, consisting of voltage, present, travel speed, and electrode kind, likewise influence porosity development. The welding method utilized, such as gas metal arc welding (GMAW) or shielded metal arc welding (SMAW), can affect porosity formation due to variations in warmth distribution and gas coverage - What is Porosity.
Results of Porosity on Weld Top Quality
Porosity formation substantially compromises the architectural stability and mechanical residential or commercial properties of bonded joints. When porosity exists in a weld, it develops spaces or tooth cavities within the material, minimizing the total strength of the joint. These gaps act as tension focus factors, making the weld a lot more vulnerable to splitting and failing under load. The existence of porosity also weakens the weld's resistance to rust, as the entraped air or gases within the voids can respond with the surrounding atmosphere, resulting in degradation in time. Furthermore, porosity can impede the weld's capability to hold up against pressure or effect, further jeopardizing the general top quality and dependability of the welded structure. In critical applications such as aerospace, automotive, or architectural building and constructions, where safety and sturdiness are paramount, the damaging effects of porosity on weld high quality can have severe effects, emphasizing the significance of reducing porosity through proper welding strategies and procedures.
Techniques to Decrease Porosity
To improve the high quality of welded joints and ensure architectural stability, welders and producers utilize specific methods targeted at minimizing the development of gaps and tooth cavities within the material throughout the welding process. One efficient approach to minimize porosity is to guarantee proper product prep work. This includes comprehensive cleansing of the base metal to get rid of any kind of pollutants such as oil, oil, or moisture that could add to porosity formation. Additionally, using the appropriate welding criteria, such as the proper voltage, present, and take a trip speed, is vital in why not try this out preventing porosity. Preserving a constant arc length and angle throughout welding likewise helps in reducing the likelihood of porosity.

Using the proper welding method, such as back-stepping or utilizing a weaving movement, can likewise aid disperse warm evenly and decrease the opportunities of porosity development. By executing these techniques, welders can effectively minimize porosity and create premium welded joints.
Advanced Solutions for Porosity Control
Carrying out innovative try this web-site technologies and cutting-edge methods plays a pivotal role in accomplishing remarkable control over porosity in welding procedures. In addition, utilizing advanced welding techniques such as pulsed MIG welding or modified environment welding can also aid reduce porosity issues.
One more sophisticated service involves using sophisticated welding devices. Using tools with built-in features like waveform control and sophisticated power resources can boost weld quality and minimize porosity dangers. Additionally, the implementation of automated welding systems with accurate control over specifications can dramatically reduce porosity defects.
In addition, integrating advanced surveillance and inspection technologies such as real-time X-ray imaging or automated ultrasonic screening can assist in detecting porosity early in the welding procedure, permitting for instant corrective activities. Generally, integrating these innovative her latest blog options can substantially enhance porosity control and improve the general top quality of welded parts.
Conclusion
In conclusion, comprehending the scientific research behind porosity in welding is crucial for welders and fabricators to create top quality welds - What is Porosity. Advanced services for porosity control can additionally enhance the welding process and ensure a strong and reliable weld.
Report this page